PLM vs PDM: Key Differences & Which One You Really Need
Have you ever heard someone throw around the terms PLM and PDM like they’re interchangeable? Yeah, same here. At first, I had no clue what the difference was either. But once I dug into it, it started to make sense. So let me break it down for you, super simple, no jargon, just the basics.
If you work in product development or you’re building anything even remotely technical, you’re going to need one of these systems eventually. Maybe even both. But which one? Well, let’s find out.
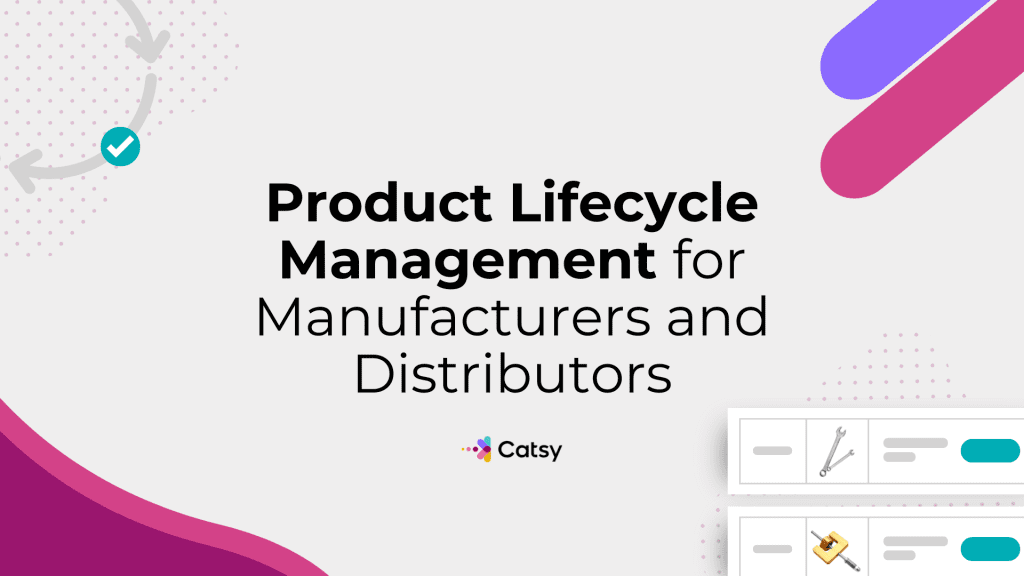
First Things First: What Even Is PDM?
So, PDM stands for Product Data Management. Think of it like a digital filing cabinet for all your product design stuff. Do you know all those CAD files, revisions, drawings, and specs? Instead of keeping them all scattered in folders, drives, or emails (ugh), PDM keeps them in one neat, secure spot.
You won’t believe this, but some teams still manage everything in shared drives, which can lead to confusion.
Here’s what PDM usually handles:
- Storing CAD files in one place
- Making sure people don’t accidentally overwrite each other’s designs
- Keeping track of all the changes (like, who edited what and when)
- Managing Bills of Materials (aka BOMs)
- Controlling who gets access to which files
Pretty handy, especially if your team’s getting bigger or you’re constantly revising stuff.
Benefits?
- No more lost files
- You avoid the whole “Wait, is this the final version?” drama
- Makes teamwork way smoother
- Helps you reuse files instead of starting from scratch
In this Article
Next, Let’s Talk About PLM
Now PLM? That stands for Product Lifecycle Management. Sounds fancy, huh? But it’s really just a more powerful system that takes what PDM does… and then goes full superhero mode.
While PDM handles files, PLM manages the entire journey of a product, from idea to design, manufacturing, selling, and even when the product is retired.
So what can PLM do?
- All the PDM stuff (yep, it’s included)
- Project management (deadlines, tasks, workflows)
- Collaboration across departments
- Regulatory compliance
- Quality checks
- Sourcing and supplier management
Basically, it’s for teams who aren’t just designing things, but also making, shipping, and selling them.
Why it’s awesome:
- Everyone’s working from the same playbook
- You get visibility across the whole product pipeline
- It helps you launch faster
- Fewer surprises during manufacturing
PLM vs PDM: So What’s the Difference?
Let’s be honest, when you’re in the middle of building, managing, and launching a product, there’s only so far a spreadsheet can take you. Every business needs to understand the difference between PDM and PLM. Whether you’re a startup managing CAD files or a global brand trying to coordinate design, compliance, and suppliers, you must start getting familiar with these systems. So here’s the real breakdown, minus the stiff tech jargon.
Make Catsy DAM and PIM Software an Extension of Your Team
Book a Free DemoScope: What Each System Actually Covers
What you need to know about PDM (Product Data Management) is that it is all about handling design data. It’s laser-focused on the early stages of product development, specifically storing, organizing, and version-controlling CAD files. PDM keeps the design department sane by making sure everyone’s working from the latest version and nothing critical gets overwritten.
PLM (Product Lifecycle Management) goes way beyond what PDM can do. It doesn’t just stop at design, it covers the entire product lifecycle. From idea to design, from manufacturing to marketing, and even through end-of-life. PLM is developed to connect every part of your business. That way your products can move through each phase efficiently and error-free.
Users: Who’s Actually Using It?
PDM is typically used by a very specific group, of engineers, CAD designers, and technical leads. They use it as they need tight control over product design files. Most engineers are in the trenches of product creation, and they need a system that helps them stay organized and in sync.
PLM, on the other hand, pulls in the whole squad. That means engineering, but also marketing, operations, quality assurance, procurement, and even external collaborators. Anyone who touches the product, from concept to customer, benefits from the centralized visibility and control that PLM provides.
Main Focus: What Each System Does Best
With PDM, the main goal is pretty straightforward: store files, manage revisions, and prevent errors. It’s like Google Drive for engineers. However, PDM comes with version control, access permissions, and a much better system for tracking changes.
PLM takes a step back and helps you see the bigger picture. Its main focus is on directing workflows and enabling cross-functional collaboration. It is there to help you manage every aspect of the product’s journey. PLM keeps everyone aligned and on task. That means it can help you change approvals and compliance checks to project timelines and supplier input.
Collaboration: Who’s Talking to Who?
PDM systems mainly support internal collaboration, especially within the engineering team. It’s great for getting designers and product engineers on the same page but usually doesn’t extend far beyond that.
PLM platforms are all about cross-functional and even cross-organizational collaboration. They make it easy to connect internal teams and external stakeholders. That means that your team and suppliers, vendors, and partners are able to communicate without much trouble. This is especially helpful if your products are complex or manufactured across multiple sites or even countries. Everyone involved has visibility into the product’s current status, no more email threads or waiting on file attachments.
Compliance: How It Handles the Red Tape
When it comes to compliance, PDM covers the basics. It helps you avoid file mix-ups and maintain a reliable trail of design changes, but that’s about as far as it goes. If you need to meet industry regulations or undergo audits, you’ll likely need to handle that manually or outside the system.
In contrast, PLM comes loaded with helpful built-in compliance tools. It allows you to audit trails, automated approval workflows, document tracking, and regulatory checkpoints with ease. All of these helpful tools can make it easier to meet standards in different industries, where compliance isn’t just nice to have, it’s legally required.
Scalability: How Far Can It Grow With You?
PDM is perfect for small to mid-sized teams. It is efficient if you need more structure but aren’t ready for full-scale enterprise systems. It’s relatively easy to implement and offers immediate benefits to engineering workflows.
But as your company grows, and especially if you’re expanding globally, you’ll probably start to hit the ceiling with PDM. That’s where PLM shines.
It’s developed to scale with your business. It does that by offering the kind of process management and visibility that growing teams, multiple departments, and international operations need. PLM gives you the control and collaboration tools to keep everything on track. It doesn’t matter if you’re managing multiple product lines or launching new markets.
The Bottom Line?
Can you imagine trying to launch a global product using nothing but spreadsheets, email threads, and guesswork? Total chaos. That’s why so many companies are moving toward PLM. It’s not just a fancy upgrade, it’s a necessary step when your business outgrows the simplicity of PDM.
That said, both systems have their place. If you’re just starting out or primarily focused on engineering efficiency, PDM can do wonders. But if you’re serious about scaling, collaborating across teams, and delivering better products faster, PLM is your next move.
When Does PDM Make Sense?
Okay, so maybe your team isn’t huge. You just need to make sure your designs don’t get mixed up. That’s a perfect use case for PDM.
You probably need PDM if:
- You mostly work with CAD files
- You’re always asking, “Who edited this?!”
- You want a safer, smarter way to store design documents
- You’re not quite ready for a massive software rollout
If you’re a mechanical engineer in a 50-person manufacturing company, your team is designing products in CAD. They probably need a reliable way to keep track of versions, changes, and access. In that case, PDM is the best option.
And When Do You Need PLM?
Here’s the thing. Once your team starts growing or you’re working across departments, PDM won’t cut it. You need a system that connects the dots between engineering, marketing, sourcing, and more.
You should go for PLM if:
- Your product goes through multiple departments
- You need better project visibility
- You’re juggling supplier info, pricing, and compliance
- You’re expanding fast and need structure
Think of a global electronics company designing a new smart device. Designers in Europe, engineers in Asia, and suppliers in the US? PLM keeps everyone synced and on schedule.
Can You Use Both?
Definitely, as a lot of companies start with PDM and grow into PLM their business needs a better system.
Here’s how it works:
- Start small with PDM for engineering
- Once the rest of the business needs to jump in, upgrade to PLM
- PLM will include your PDM tools, but go bigger and broader
It’s kind of like leveling up. You don’t need to go full-blown PLM from day one. Build as you grow.
Quick Quiz: Which One Do You Need?
Ask yourself:
- Who needs access to product info? Just engineering, or more teams?
- Are we worried about compliance or audits?
- Is project coordination a mess?
- Are we scaling fast?
If your answers lean toward “just engineering,” go with PDM. If you said yes to any of the others? Sounds like you’re ready for PLM.
What do you think? Still unsure? Keep reading.
The Bigger Picture: PLM, PDM, and Digital Transformation
When managing any business, it’s easy to get confused between tools like PLM, PDM, and PIM. While they may sound similar, each serves a different purpose.
PLM (Product Lifecycle Management) is used in the early stages of the product development process. Sketches and materials as well as approvals and timelines can be managed through PLM.
PDM (Product Data Management) usually works closely with PLM to ensure that each product data version is saved. PDM focuses on storing and organizing technical product files, like size charts.
PIM (Product Information Management) is used once your product is ready to sell. Each product needs to have specific details so your customers know what they are buying. PIM ensures that your product listings are accurate and up to date.
To summarize it all, PLM and PDM are great for developing your product, while PLM is essential for marketing and selling it effectively.
If you’re still growing? Start with PDM. But keep PLM on your radar. If you’re already dealing with cross-functional chaos? PLM might be the answer you’ve been waiting for. Now is the best time to make your product data smarter, faster, and way easier to manage.
Catsy helps teams centralize and manage their product content from start to finish. Want better version control? Need to sync product info across platforms? We’ve got your back.
Book a demo with Catsy and see it in action.
Want more tips, tutorials, and insights on product content and e-commerce operations?
Stay connected. We post regularly to help brands like yours scale smarter.
Are You Ready To streamline your product content management?
Continue Reading
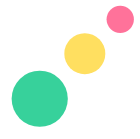
Frequently Asked Questions
PDM (Product Data Management) is focused on handling product design data, like CAD files, drawings, and version control. On the other hand, PLM (Product Lifecycle Management) covers the entire product lifecycle, from idea and design to manufacturing, marketing, compliance, and even end-of-life. It’s a much more holistic, business-wide system that connects all the dots beyond engineering.
PDM (Product Data Management) is focused on handling product design data, like CAD files, drawings, and version control. On the other hand, PLM (Product Lifecycle Management) covers the entire product lifecycle, from idea and design to manufacturing, marketing, compliance, and even end-of-life. It’s a much more holistic, business-wide system that connects all the dots beyond engineering.
PDM systems are generally more affordable because they’re more limited in scope. They’re perfect for small teams or companies focused on engineering workflows. PLM systems cost more upfront, but you’re also getting a lot more functionality, like compliance tracking, multi-team collaboration, and scalable workflow management. If your business is growing or dealing with more complex operations, PLM often pays for itself in efficiency gains.
Yes, there are a lot of them. Most modern PDM and PLM systems now offer cloud-based versions, which means you don’t need heavy on-premise infrastructure. Cloud solutions are easier to scale, update, and access remotely, making them ideal for hybrid teams, remote workers, or companies working with external partners and suppliers. Some even offer mobile apps so you can check approvals and updates on the go.
PDM is usually used by engineers, designers, and technical teams, basically anyone dealing with CAD files and product design data on a daily basis. It’s their go-to system for keeping track of file versions and preventing design mix-ups.
PLM is used by a much wider group, including engineering, marketing, procurement, quality assurance, and operations. It acts as a central hub where everyone involved in a product’s journey can collaborate, track changes, and stay aligned.
Subscribe For More Content
Sign up for monthly tips on how to drive revenue with product content.